この資料は、
TPiCSの基礎講座や、研修会を受講され、基本的な操作方法やおおよその機能をご理解いただいた方に、その先の“ものづくり”の視点から、アイテム構成の要点を捉えて、マスター構築のヒントにしていただくためのものです。
このサンプルは、量産で繰返し性のあるボルトをモデルにしています。
見込みで生産計画を立て、
- 製造ロット数で数量をまとめたり
- 一定期間の必要量をまとめたり
- 生産上限数を超えないように数量を前倒しする設定が行われており
- 工程や材料の特性に合わせた生産計画を立てられる
ようにしています。
また、生産能力をオーバーした際は、別の設備や外注先に計画を割り当てできるようにしており、別の設備は手動機のため、通常の自動機と工程を変更することや、外注先に加工依頼する際は外注先で材料を自己調達しているため、材料を使用しないようにマスター設定しています。
社内加工や外注加工内の中間工程では在庫を余らせない前提のモデルなので、中間工程をアイテムではなく詳細工程で設定して、作業指示書発行と生産実績入力を詳細工程毎に行い、どの工程まで進んでいるのか進捗を取れるようにしています。
なお、当モデルは鍛造や表面処理の工程がメインとなりますが、材料や工程を変更すれば金属加工共通のサンプルとしてご使用いただけます。
フランジボルトとは
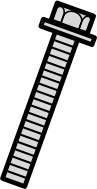
フランジボルトとは、
フランジと呼ばれる薄い円形のつばがねじ頭部の底面にくっついており、座金(ワッシャー)を組み込む必要がないネジです。座面が付属するために緩みが生じにくく、座金を組む手間が省けるのが利点です。
また、フランジボルトは六角ボルト比べて母材との接触面積が広いため、締め付けトルクが円形に広がり、均等に締め付けられます。その結合力の高さ、分解の容易性から自動車や各種製造装置などの産業用製品まで幅広く使用されています。
製造工程
ボルトの製造方法には、金属の丸棒を切削して製造する方法と、金型を使用して圧造する方法がありますが、量産、規格品のほとんどは圧造(冷間圧造)して製造されます。
コイル状の素材を常温のまま、①伸線 → ②頭部圧造(ヘッダー) → ③ネジ転造(ローリング)して素のボルトを成形します。ナットも同様に線材から ①成形(冷間圧造)→ ②ネジ切り(タッピング)して素のナットを成形します。
その後、素のボルトとナットを強く・硬く・粘り強くするために熱処理を施します。
さらに表面の耐食性や硬度、装飾性などを向上させるためにクロムなどのメッキを施して製品が完成します。
生産のポイント
これは、 架空の生産管理ポイントです。
- 自動ライン、手動ラインによって工程が変わる。
- 社内、外注で子アイテム(線材)が変わる。
- 製品構成表で最終製品のボルト、ナットの使用量は本単位、ボルト、ナットの加工の使用量はkg単位で管理(構成表の換算)。
- 外注加工品の初工程である支給工程の実績を登録すると、社内加工品の在庫を引落しする。
- 外注加工の計画は期間で計画をまとめ、社内加工の計画は日の生産上限数を超えないように前倒しする。
製品構成
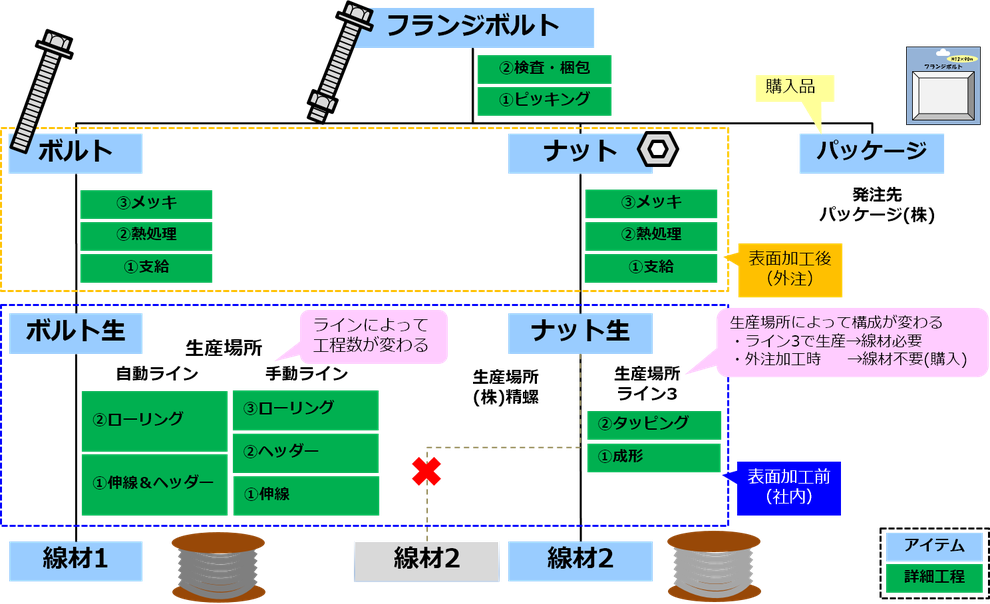
製品構成ツリー
①[業務メニュー]-[マスター管理]-[アイテムマスター]を開きます。
②サイドパネルの[構成ツリー]で製品コード”FB45M12_CR_PACK”を選択して構成ツリーを表示します。
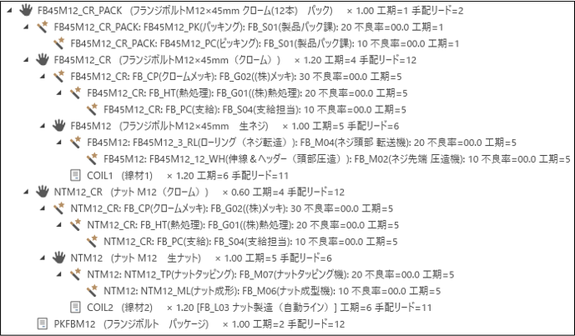
使用しているシステム、オプション
CSVデータは、アイテム件数50件以内に抑えており、デモ版で試すことができます。
50件を超えて使用する際には以下のオプションが必要になります。
- 繰返生産システム(fMRP)
- 複数ロケーションオプション
- 着手信号機オプション
- 受注販売管理オプション
フランジボルトの生産管理を再現する操作手順
事前準備
[データベース設定ツール]-[テーブル設定]-[文字項目の桁数、項目数]で、「作業コードの桁数」の「設定値」を“13”に変更し、[文字項目の桁数を適用]ボタンを実行する
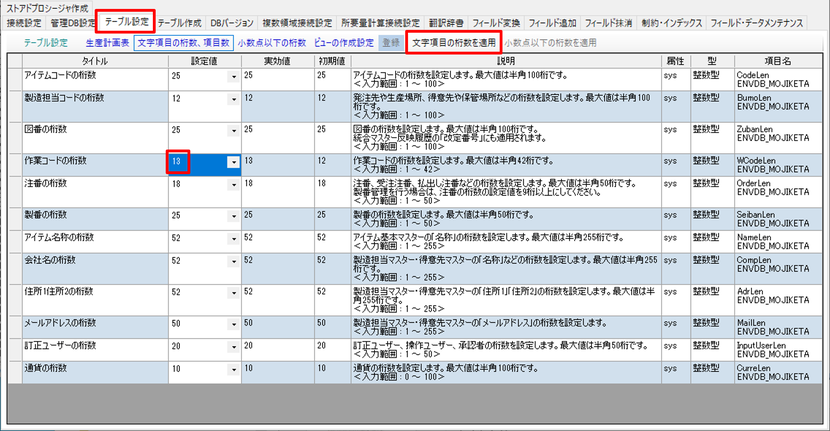
データの読込みとマスターの構成ツリー確認
-
[定形処理]-[テキストファイル読込み]でフォルダ選択後、[読込み開始]ボタンで以下のCSVファイルを読込みします。
読込むファイル:
TXBAIK.csv
TXCALE.csv
TXCUST.csv
TXHEAD.csv
TXITEM.csv
TXJIKA.csv
TXKOUT.csv
TXPRTS.csv
TXSECT.csv
TXTANK.csv
TXWORK.csv
TXZAIK.csv
※[Ctrl]+[R]で読込みすると、既存データをすべて削除してから読込できます。
通常は全部データが消えてしまうため、テスト環境でのみの読込方法です。 - アイテムマスターや構成ツリーで構成を確認します。
生産計画作成
①[計画業務]-[生産計画表]を開き、右クリックメニューの[データ管理]-[起点レコード作成]を行います。
②製品コード”FB45M12_CR_PACK”のレコードを選択し、右クリックメニューの[データ管理]-[見込み行作成]-[選択レコードのみ]を実行して見込行を追加します。
③製品コード”FB45M12_CR_PACK”の見込行に、4/12に300パック、4/15に400パックを入力して、[所要量計算]ボタンで所要量計算を実行します。
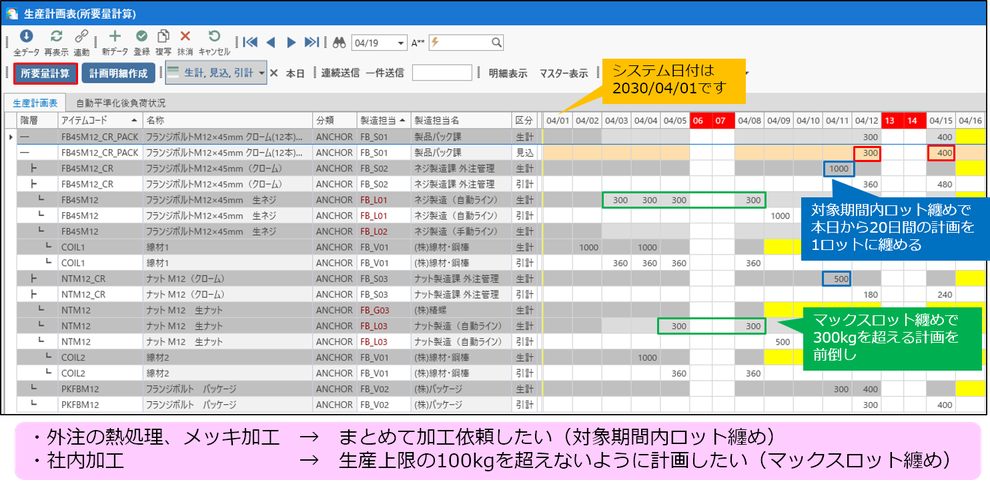
計画調整
①ボルト(FB45M12)の「ネジ製造(自動ライン)」の生計を「ネジ製造(手動ライン) 」にドラッグ&ドロップで移動します。
②ナット(NTM12)の「ナット製造(自動ライン) 」 の生計を「(株)精螺」にドラッグ&ドロップで移動します。
③[所要量計算]ボタンで所要量計算を実行します。
④[計画明細作成]ボタンで計画明細を作成します。
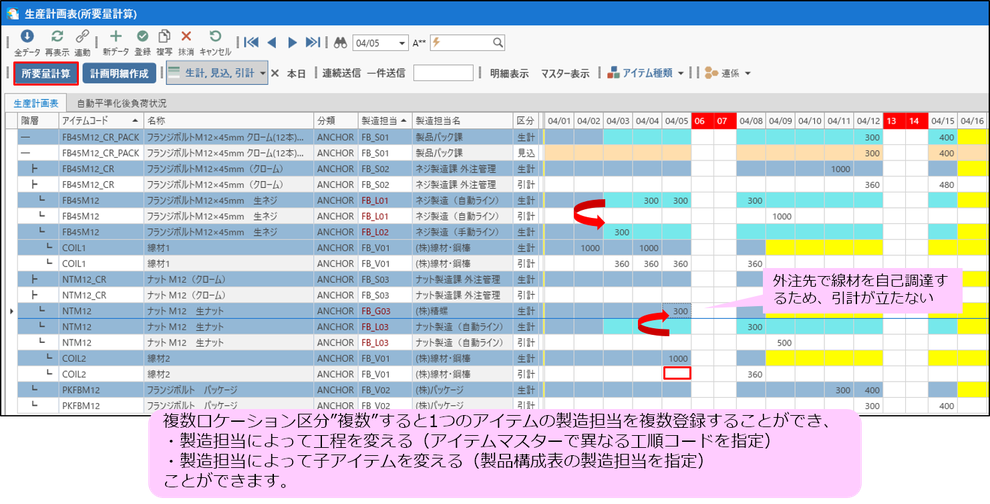
計画明細データの確認
[計画明細データ手入力]で作成された計画明細データを確認します。
実績入力できるように、右クリックメニューの[データ管理]-[印刷済みへ更新(全データ)]で印刷済み扱いにします。
(実運用では、注文書発行や作業指示書発行画面で印刷、メール送信すると印刷済みになります)
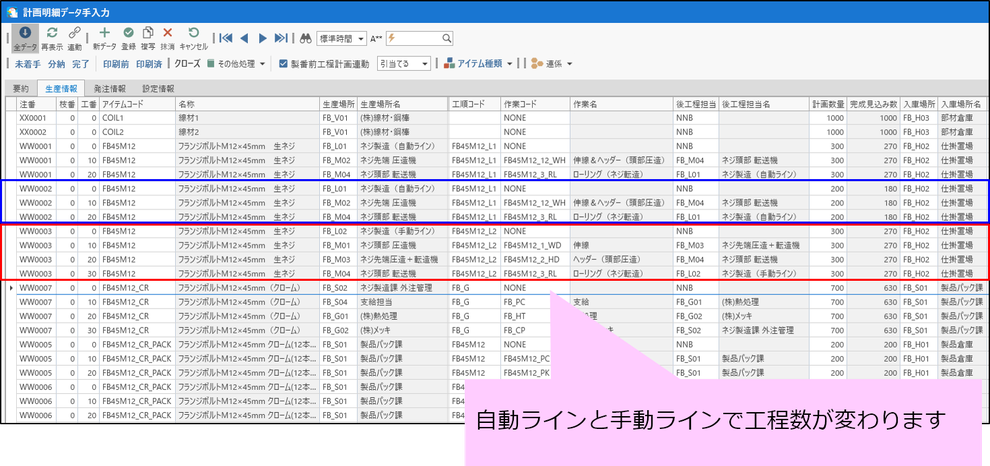
検収実績登録
[資材検収実績入力]で購入品(線材、パッケージ、生ナット)の検収実績を登録します。
実績入力すると、購入品の現在在庫が増えるので[現在在庫一覧]で確認します。
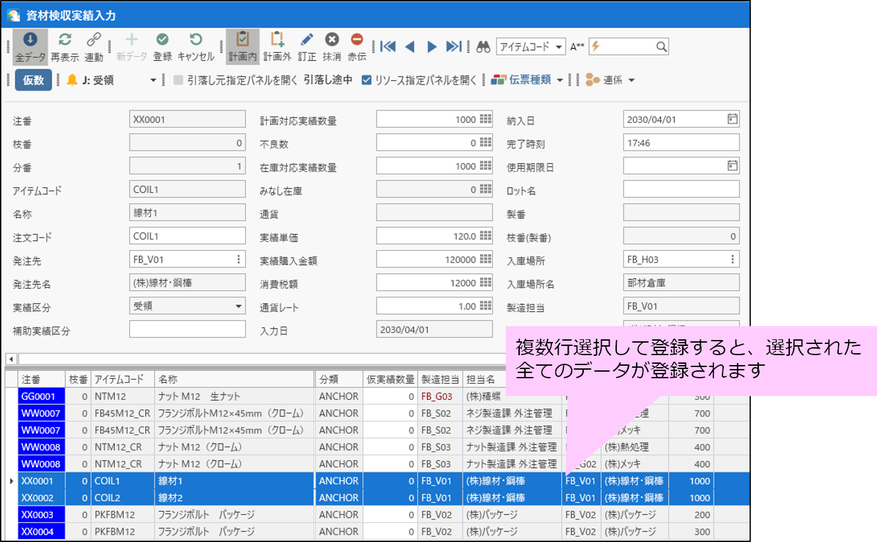
生産実績入力(初工程)
[着手信号機]から社内加工(初工程)の生産実績を登録します。[生産業務]-[着手信号機]-[着手信号機の設定]の『着手信号機でデータ表示時に全ての「着手可」を計算する』設定をオンにすると、着手可項目でソートできます。
初工程(工番=10)の実績入力すると、線材の現在在庫を引落して、社内工程アイテムの仕掛在庫が計上されます。
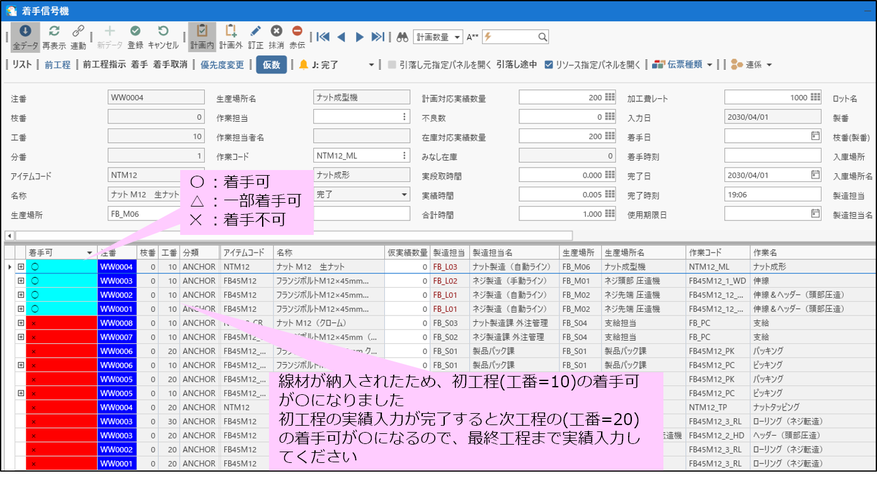
在庫確認
[現在在庫一覧]で現在在庫を確認します。
検収実績入力により線材の現在在庫が増え、親アイテムの初工程(伸線&ヘッダー)の生産実績を登録すると、線材の在庫を引落しして、親アイテムの仕掛在庫が計上されます。
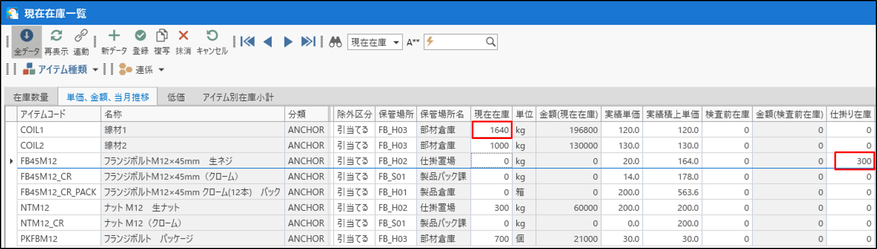
生産実績入力(最終工程)
[着手信号機]から社内加工(最終工程)の生産実績を登録します。親アイテムの最終工程(ローリング)を実績入力すると、工程元実績パネルが開くので[実行]ボタンを押して登録します。
[現在在庫一覧]で初工程(工番=10)の実績入力で計上された仕掛在庫が減算され、現在在庫が加算されていることを確認してください。
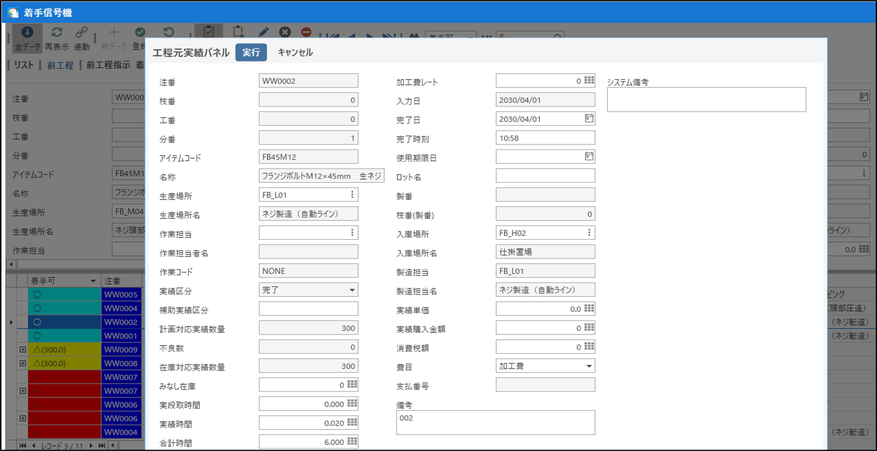
外注加工実績入力
[資材検収実績入力]で外注加工実績を熱処理→メッキの順に登録します。
外注加工の検収実績が全て登録されると、外注加工アイテムの現在在庫が増えるので、[現在在庫一覧]で確認してください。
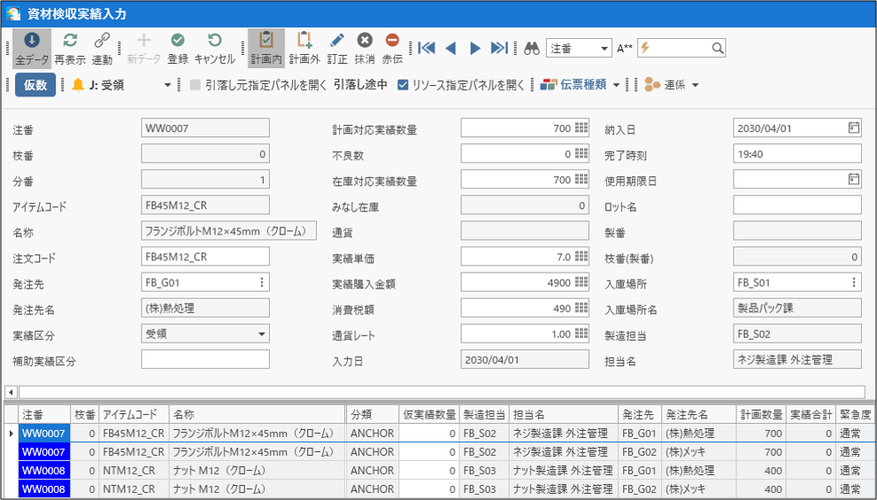
製品実績入力
[着手信号機]で製品の実績を登録します。
初工程のピッキングの実績入力で外注加工アイテムの現在在庫を引落して製品アイテムの仕掛在庫が計上され、最終工程のパッキングの実績入力が行われると現在在庫が計上されます。[現在在庫一覧] で確認してください。
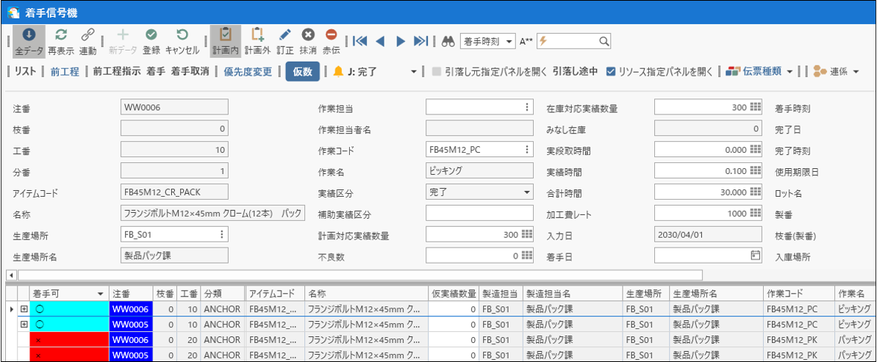
進め方のヒント
■出荷までの操作
- 得意先マスターと売価マスターを登録する。
- [受注データ入力]から受注入力する。
-
[出荷実績入力]で製品在庫を出荷する。
計画立案→部材発注→検収実績→作業指示→生産実績→受注→出荷までの一連の流れが確認できます。
■計画やマスターをいろいろ変えて試してみましょう。
例えば
- 見込みの数量を変える。連続する計画を立ててみる。
- マックスロットサイズ、対象期間内ロット纏設定を変えてみる。
-
社内工程、外注加工工程アイテムの実績入力時、不良数を入力してみる。
→不良率10%を設定しているため、計画に対し10%の不良が発生しても所要量計算で補充が掛からない。 - ピッキングや支給を詳細工程に登録しているが、払出管理に変更してみる(払出管理オプション必要)。
- 部門別ガントチャートで負荷を確認して計画調整してみる(計画調整は部門別ガントチャートオプション必要)。
- 製品の出荷まで完了したら、製品別原価集計で標準原価と実績原価を比較して、予定の原価と実際の生産の原価の差を確認する。